The cooling time of plastic pallet injection molding accounts for about 80% of the entire injection molding production cycle. Plastic tray cooling time varies with wall thickness, molten plastic tray temperature, demolding temperature and injection mold temperature. Poor cooling often results in warpage or surface defects that affect the dimensional stability of the product. The 100% accuracy of the formula for calculating the cooldown time for all locations has not been published, but only under appropriate assumptions about the base length. Since the definition of cooling time is different, the formula is also different.
There are three commonly used cooling time reference standards as follows.
(1) The time required for the temperature of the center layer of the thickest part of the injection pallet mould wall to cool below the thermal deformation temperature of the plastic pallet;
(2) The temperature of the center layer with the thickest wall of the crystalline plastic disc molding part, the time required to cool below the melting point, or the time required to reach the specified crystallization percentage.
(3) The temperature in the section of the plastic tray injection molded part is uniform, and the cooling time reaches the specified product mold temperature;
In the formula, the following assumptions are generally made:
1. The plastic tray is injected into the injection mold, and the heat is transferred into the injection mold to cool.
2. The plastic tray in the mold cavity is in close contact with the mold cavity and is separated without cooling and compression. There is no heat transfer and flow resistance between the melt and the mold walls. That is, when the plastic pallet is filled into the mold cavity, the surface temperature of the workpiece is equal to the mold wall temperature.
3. During the cooling process of the plastic tray injection molded parts, the surface temperature of the injection mold cavity is always kept uniform.
(The melt filling process is an isothermal process, and the material temperature is uniform)
The influence of the orientation and thermal stress of the plastic pallet on the deformation of the workpiece is negligible, and the size of the workpiece has no effect on the solidification temperature.
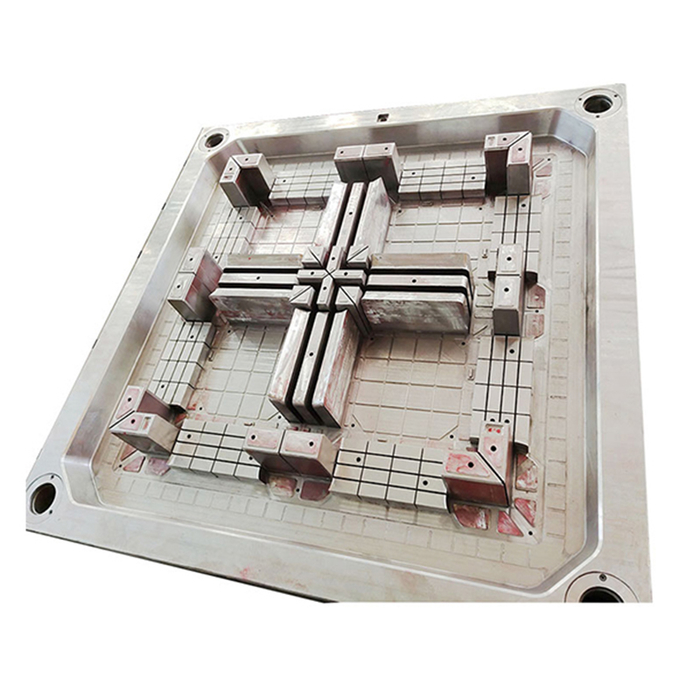
Smooth Surface Plastic Pallet Mould
Usage:
Plastic pallets are commonly used for the commercialization of high rotation and/or bulky products. These pallets reduce the risk of damaging a product by moving it from one point to another. This is because you will only lift the platform without touching the product.
Advantage of plastic pallet:
easier to transport.safer for everyone.take up less space.more flexible and versatile.have a longer lifespan than wood pallets.
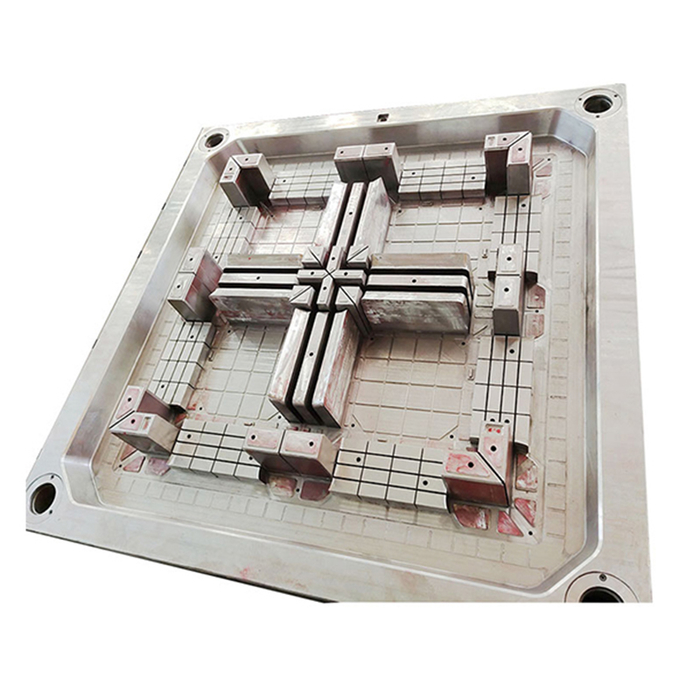
Smooth Surface Plastic Pallet Mould
Usage:
Plastic pallets are commonly used for the commercialization of high rotation and/or bulky products. These pallets reduce the risk of damaging a product by moving it from one point to another. This is because you will only lift the platform without touching the product.
Advantage of plastic pallet:
easier to transport.safer for everyone.take up less space.more flexible and versatile.have a longer lifespan than wood pallets.