Plastic Pallet Mould Processes
If you are looking to manufacture plastic pallets, you will find a variety of plastic pallet mould options available. Using a plastic pallet mould can help you create quality, durable pallets that can withstand rough handling. The process can include High-pressure injection molding, Rotating moulding, and Thermoforming.
High-pressure injection molding
High-pressure injection molding of plastic pallet mould is a process that uses heat to shape plastics. It is suitable for large-scale production where the same design is repeated many times. Plastic pellets are fed into the machines through a hopper. The plastic enters a heating chamber and exits through a nozzle. The plastic then cools and hardens inside the mould cavity.
The plastic pallet's top surface is flat and the bottom surface is reinforced with ribs that are 3 mm thick. The injection molding draft angle varies the thickness of the ribs, but the general rule of thumb is to keep the ratio of flow length to rib thickness below 150. The run length of the melted polymer ensures that the plastic pallet's melting state is maintained throughout the injection process.
High-pressure injection moulding is a process in which a plastic granulate is melted into a thick liquid and injected into a tempered plastic mould at high pressure. It is a versatile process for producing large quantities and consistently high-quality products.
Thermoforming
Thermoforming is a process in which plastic sheet is heated to make it pliable and stretchable. This plastic sheet is then stretched over a mould, and then a force is applied to form the shape. This method is often used to produce car parts, such as instrument panels, tail lights, consoles, door panels, and pallets. It is advantageous because it eliminates the need for expensive tooling. Also, the process can capture more texture than other plastic forming processes.
Thermoforming plastic pallets are safe, non-toxic, and recyclable. However, the process is not without its challenges. The most important step in the process is the design of the thermoforming plastic pallet mould, which must accurately reflect the desired plastic pallet shape. This process requires careful planning and design, and there are a few guidelines that should be followed to ensure that the plastic pallet mould is a success.
Thermoforming plastic pallet mould benefits: Compared to injection molding, it creates larger parts at lower costs. The tooling is usually half as expensive, and costs less per piece. Also, the process is versatile, as it can be used to create larger, thicker packaging. The process can also be used to create custom-sized packaging for a variety of purposes, including consumer goods and toys.
Structural foam molding
Structural foam is a type of composite material made of polymers. It is usually thermoset but can also be thermoplastic. It is manufactured by molding the polymer with an inert gas or chemical blowing agent. This type of plastic is lightweight, durable, rigid, and impacts resistant. This type of plastic pallet mould is a good choice for many applications.
Structural foam molding is especially suitable for manufacturing large, 3-dimensional products with limited side actions or undercuts. This type of molding also offers cost savings, since it can be produced with a cast aluminum mould and requires less tooling. Tooling costs can run into the hundreds of thousands of dollars. Moreover, cast aluminum molds are often used for structural foam products, because they are cheaper and have a shorter lead time.
The process of structural foam molding involves introducing a blowing agent such as nitrogen gas into the plastic. This blowing agent helps the plastic to form a sandwich-like structure. The structure consists of a solid outer layer and a foam core in the center. Structural foam parts are light and rigid and exhibit minimal bending. Moreover, they have a higher weight capacity.
Rotating moulding
Rotating plastic pallet moulding is a process where plastic material is injected into a mould under pressure. The plastic then cools and is ejected from the mould in the shape of a pallet. It is lightweight and can be used to transport goods, and has a cellular core surrounded by a rigid material. The process produces pallets that are typically ten to thirty percent lighter than solid plastic.
Single Face Forklift Pallet Mould
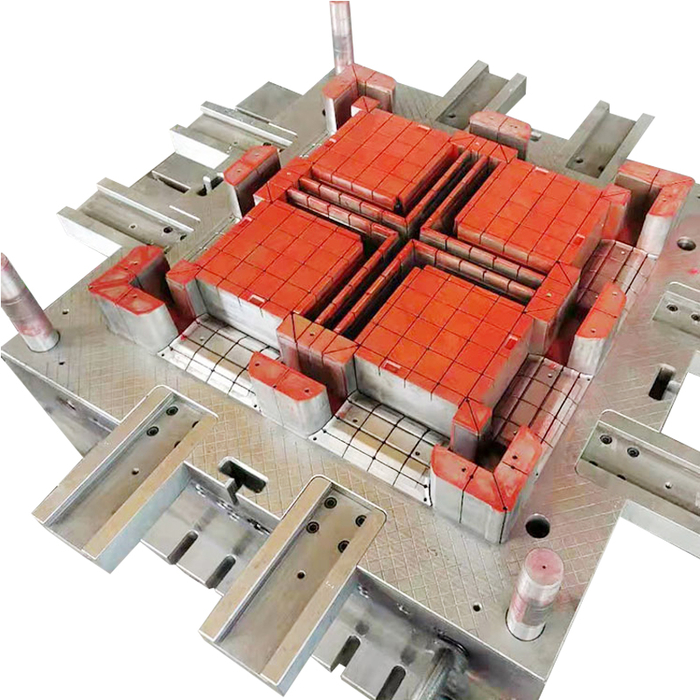
Single Face Forklift Pallet Mould
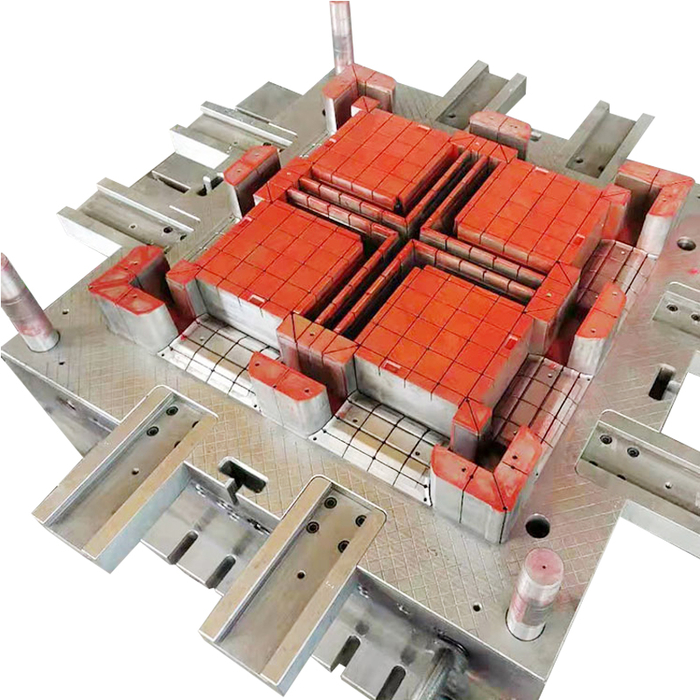
Usage:
Plastic pallets are commonly used for the commercialization of high rotation and/or bulky products. These pallets reduce the risk of damaging a product by moving it from one point to another. This is because you will only lift the platform without touching the product.
Advantage of plastic pallet:
easier to transport.safer for everyone.take up less space.more flexible and versatile.have a longer lifespan than wood pallets.