Whether you want to create a new plastic pallet mould or repurpose an existing one, there are a variety of different plastic pallet molding options to suit your needs. You can use compression and rotational molding techniques to produce pallets. You can also find structural foam moldings that can create custom molds for your pallets. These are great ways to customize your trays and get a unique look.
Typically, compression molding is the process of preheating polymers to high temperatures before applying them to a mold. This results in a strong composite part with good stiffness. It is used in a wide range of applications including aerospace, medical, fuel and accessories.
Thermosets are the most commonly used materials for compression molding. These plastics have excellent impact and abrasion resistance. They are also known for high melt viscosity and good low temperature impact strength. HDPE is one of the most popular types of plastic used for compression molding.
Another material used in compression molding is an elastomer. This is a rubber-like material that is popular for its ergonomic and biocompatible properties. Commonly used in cylinder diaphragms, shock absorbers and lip seals. It is also used in medical devices such as orthopedic implants.
To produce a part using compression molding, the process begins with weighed raw materials. It is then placed into a heated metal mold. During the molding process, the heat used to soften the polymer allows the material to conform to the shape of the mold. The resulting finished product has a smoother surface finish. Trimming or cutting is usually done after shaping is complete.
After the molded part completes the molding cycle, the excess charge is expelled from the cavity. This results in a lot of waste. Most compression molding is done automatically, but it is sometimes performed by humans. If the machine does not require a lot of manual labor, it may be possible to automate the entire process.
Thermosets can be molded with varying levels of machining. Typically, compression molding machines open along a vertical axis, but some presses have lighter pneumatic systems. Molds can be made of steel or aluminum. During the molding process, the molding machine's heating and cooling systems regulate the temperature of the molded plastic so that it remains at the interface.
The molding temperature depends on the properties of the plastic material. The melt viscosity of the thermoset will determine how long it takes to heat the material. Some of the most common materials include HDPE, Nylon, Polypropylene, PEEK, and SMC. Some composite materials, such as fiberglass mat-reinforced thermoplastics, can be used for compression molding. They are popular for their excellent mechanical and impact resistance.
Other materials used in compression molding are elastomers, plastics, and polyvinyl chloride. These additives improve the molding process.
The most commonly used compression molded materials are thermoset composites. It's a complex mixture of resins combined with fibers. This is especially useful for compression molding of complex shapes and strong parts. It is also used in automotive applications.
Among the many types of plastic pallets, rotomolded plastic pallets are considered the most durable. They are made of double walled HDPE construction and are very hygienic. They have built-in protection against germs that can harbor on wooden pallets and damage the product. They also have excellent impact resistance. They are extremely durable and suitable for cold chain supply procedures. Despite their durability, these plastic trays are lightweight.
There are many processes used to manufacture these trays. Injection molding is one of the most popular methods. The process is quick and produces precise, durable plastic pallets. Ideal for large manufacturing companies. It can also be used to create complex designs.
Another method is thermoforming. In this process, plastic powder is placed in a heated hollow mold. The powder is then continuously rotated to ensure an even distribution. Afterwards, the mold is rotated again to distribute the resin on the inner walls of the mold. The resin is then weighed before placing it between the mold halves. It is then heated to a predetermined temperature. When the proper temperature is reached, the molten plastic is injected into the mold. It is then allowed to cool and harden in the cavity. The resulting plastic tray has a honeycomb structure with dense walls and a core.
The rotational molding industry started in the 1940s. These companies produce a wide range of products, including custom plastic pallets and intermediate bulk containers. They also produce a variety of novelty items such as children's toys, mannequins and hollow displays.
Other companies specialize in standard plastic trays and laundry carts. They also produce custom rotomolded plastic bins and material handling containers. Some of the industries they serve include aerospace, automotive, food and beverage, retail and pharmaceuticals. Some companies also specialize in specific applications, such as medical backsheets and trash cans.
While rotationally molded plastic trays are durable and hygienic, they are also lightweight. They are less expensive and require fewer tools than other plastic molding processes. They are also known for being highly reusable and long-lasting. They have an excellent strength-to-weight ratio, making them a popular choice for a wide range of applications.
These pallets are commonly used in racking systems in warehouses. They are available in a variety of standard colors and sizes. They are also moisture resistant and non-porous. Their glossy finish provides a high-quality finish. They are also used by the US Postal Service.
It is well known that rotomolded pallets have the highest life-to-cost ratio. They are able to withstand higher load capacities than injection molded pallets. They have good impact resistance and can withstand temperatures up to 40 degrees Celsius. This is a huge advantage for customers who require products that can be shipped by cold chain suppliers.
Structural foam molding is cheaper and faster than conventional injection molding processes. It can also be used to produce parts of various thicknesses. For example, it can be used to produce thicker bosses, ribs and walls. It can also be used to produce components with a honeycomb core for improved impact resistance.
The process uses low pressure and chemical blowing agents to fill the mold. The pressure is much lower than traditional injection molding, which makes the tooling cost cheaper and the infrastructure smaller. In addition, the finished part is less dense and lighter in weight. This means manufacturers can create large parts with less assembly time.
The resin is mixed with nitrogen to create a chemical reaction. This reaction forces the plastic into the cavity. Inert gases also reduce the weight and density of the finished product. The resulting product is lightweight, rigid, and has a honeycomb structure. This helps prevent shrinkage and warping.
Additionally, the process produces a porous foam core. This provides impact resistance and better sound insulation. It can also be used to replace sheet metal, fiberglass and concrete. Typical applications include shelving systems, pallets and products requiring high load capacity. Finished plastic pallets are lightweight and strong, and offer similar benefits to injection molded plastic pallets.
Inject the resin into the pre-prepared mold. It can be manufactured using a variety of resin classes, allowing for customized products. The performance of the resin depends on the specification of the part. Resins also need to be compatible with additives.
Structural foam molding for plastic pallet molds is typically less costly than conventional injection molding. It can also be produced with fewer post-production processes. Unlike the injection molding process, structural foam molding does not require steel molds or hot runner systems. It can be manufactured in aluminum moulds. In addition, the material's lighter weight and lower density allow for more impact-resistant parts.
The use of structural foam for plastic pallet molds allows manufacturers to reduce the overall weight of plastic pallets. It also means that the resulting product is less likely to sink into ribs, large cross-sections or other structures. It is ideal for products that need to be exposed to temperatures ranging from cold to hot.
Structural foam molded articles have a high strength-to-weight ratio. This means they are less prone to damage and can be used in high stress applications. They are also dimensionally stable. During this process, there is almost no thermal expansion, ensuring stress-free parts.
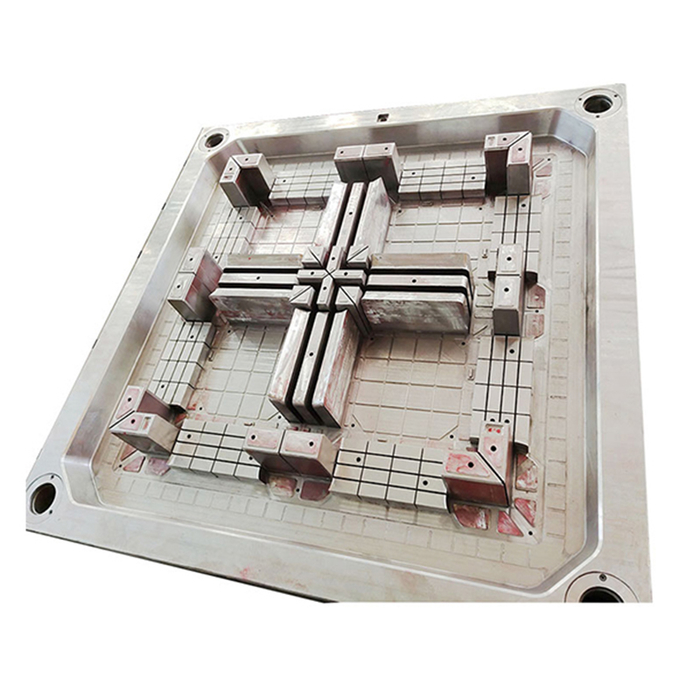
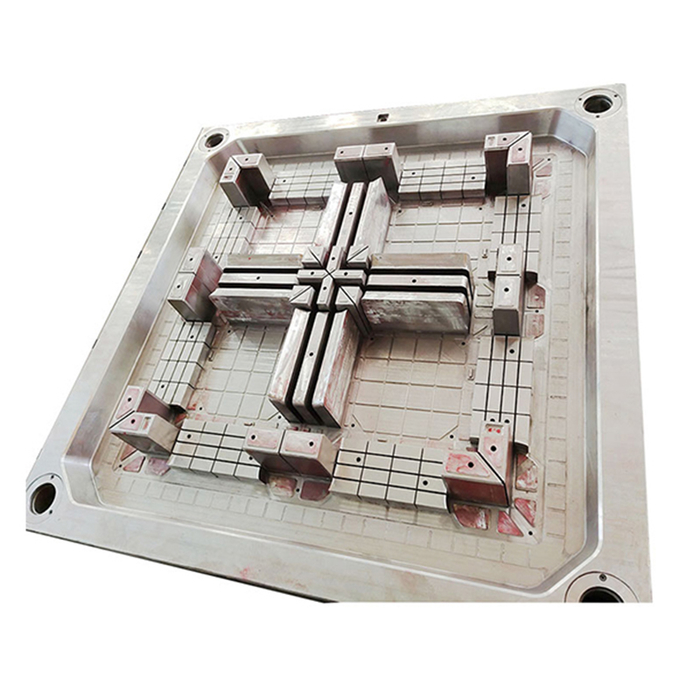
Usage:
Plastic pallets are commonly used for the commercialization of high rotation and/or bulky products. These pallets reduce the risk of damaging a product by moving it from one point to another. This is because you will only lift the platform without touching the product.
Advantage of plastic pallet:
easier to transport.safer for everyone.take up less space.more flexible and versatile.have a longer lifespan than wood pallets.