Wang Mould is a professional supplier of pallet moulds. From the three-dimensional modeling of the product to the first trial of the mold, we strictly control the manufacture of every step and insist on making high-quality molds. Here are the steps we take to make a pallet mold:
1. 3D design analysis of plastic pallets
After we receive the customer's product design, we will immediately convene all relevant technical personnel to analyze its shortcomings and problems that may be encountered during processing. For example, the demolding slope, strength, plastic filling, deformation, wall thickness, skin texture, etc. are analyzed. After these discussions, a mold flow analysis is carried out, and if any problems arise, we will immediately get in touch with the customer and provide solutions or suggestions.
2. Plastic tray mold design technical meeting
All relevant personnel will participate in the new mold design technical meeting. At the meeting, we will put forward all the technical points, such as: the use of steel materials for mold parts, the basic structure of the mold, the plastic material and its melt index, the special requirements of customers, the parameters of the injection molding machine and the processing steps of the parts and so on.
3. Plastic tray mold design and inspection
After the pallet mold is designed, the mold design review department will review the design. These audits include: Mold structure inspection Mold movement and guide system inspection Mold injection system inspection Mold cooling system inspection Mold ejection system inspection Mold vulnerable parts inspection.
4. Inspection of plastic pallet mold steel
After the design of the tray mold is confirmed by the customer, we start sampling and testing the steel material with high-quality testing equipment to ensure that there are no cracks or impurities. And the steel hardness tester can measure whether the hardness of the steel is qualified or consistent.
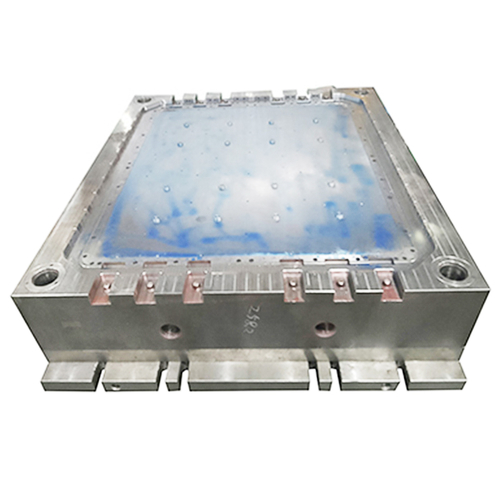
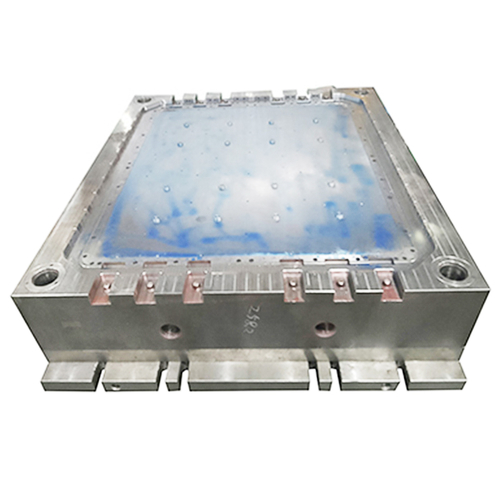