Maintenance of molds before production
The surface of the mold must be cleaned of oil and rust, and the cooling water holes of the mold must be checked for foreign objects and water passages.
It is necessary to check whether the arc in the mold mouth sleeve is damaged and whether there is any residual foreign matter.
Whether the screws of the fixed template of the mold and the clamping clamp are tightened, etc.
After the mold is installed on the injection machine, it is necessary to run the empty mold first. Observe whether the movement of each part is flexible, whether there is any abnormal phenomenon, whether the moving parts such as guide post, ejector rod and row position are worn, whether the lubrication is good, whether the ejection stroke and opening stroke are in place, and whether the parting surface matches when the mold is closed. strict and so on.
Maintenance of molds in production
When the mold is in use, it is necessary to maintain the normal temperature, and it cannot be hot or cold. Working at normal temperature can prolong the service life of the mold.
Check all the guide posts, guide sleeves, return needles, push rods, sliders, cores, etc. of the mold for damage every day. Observe at any time, check regularly, scrub in time, and regularly refuel and maintain them, and maintain them on and off work every day. Twice to ensure flexible movement of these sliders and prevent tight bites.
Before each mold clamping, you should pay attention to whether the cavity is cleaned, and no residual products or any other foreign objects are allowed to be left. It is strictly forbidden to use hard tools during cleaning to prevent the surface of the cavity from being bruised.
For molds with special requirements on the surface of the cavity, the surface roughness Ra is less than or equal to 0.2cm. It must not be wiped with hand or cotton. It should be blown with compressed air, or wiped gently with high-grade napkins and high-grade absorbent cotton dipped in alcohol.
Regularly clean the parting surface of the mold and the foreign body glue, foreign body, oil, etc., and clean the parting surface and the runner surface twice a day. During the molding process, the injection mold often decomposes low molecular compounds to corrode the mold cavity, making the bright cavity surface gradually dull and reducing the quality of the product, so it needs to be scrubbed regularly, and alcohol or ketone preparations can be used for scrubbing. Dry in time after scrubbing.
Regularly check whether the waterway of the mold is unobstructed, and fasten all the fastening screws.
Check whether the limit switch of the mold is abnormal, whether the inclined pin and the inclined top are abnormal.
King Mould is a plastic pallet mould manufacturer, which has won a high reputation from customers with excellent technical resources, reasonable prices, timely delivery and perfect after-sales service.
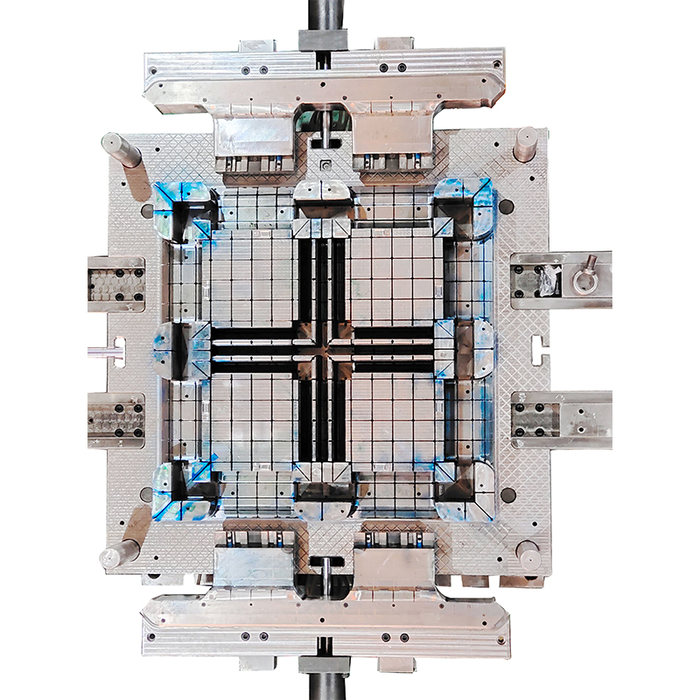
King Mould is a plastic pallet mould manufacturer, which has won a high reputation from customers with excellent technical resources, reasonable prices, timely delivery and perfect after-sales service.
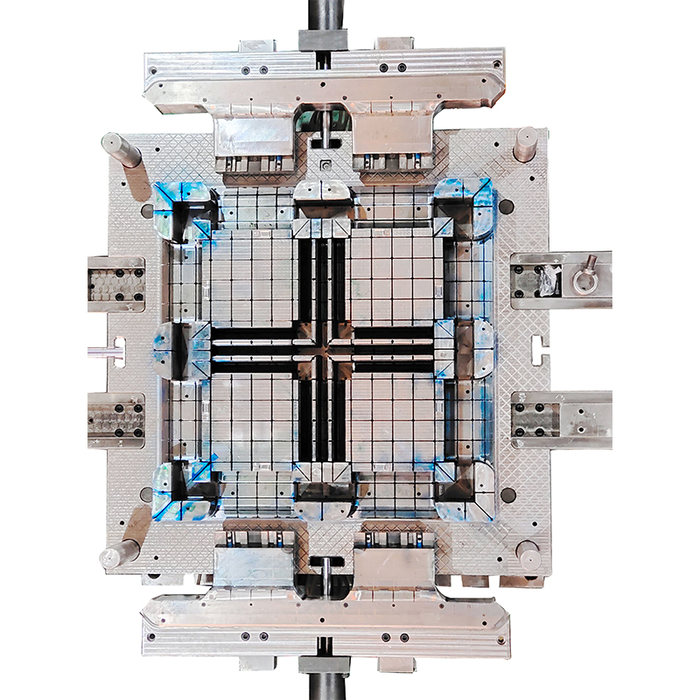
Heat Treated Single Face Pallet Mould
Place of Origin:Zhejiang, China
Business Type:Manufacturer, Exporter
Brand Name:KING MOULD
Product Material: PP
Product: Industrial product
Mould design software:UG,PRO-E,SOLIDWORKS,CAD,etc
Mould features: Full automatic production line
Mould material: P20, 718
Runner System: Hot Runner
Heat Treatment: Nitriding(based on your request)
Mould Base:45#,S50C or according to customer's requires
T1 sample time: 45-85 days
Price: Negotiated
Offer After sale service:Yes
Payment Terms:T/T
Can offer:OEM/ODM sevice, accpet for injection production
Application:widely used in petrochemical, chemical,, beer, drinks, food, machine, tobacco etc.