What are the plastic pallet mould production equipment and machines? For the future trend of the automated pallet production line, there are already signs of intelligent development.
Many large-scale plastic pallet manufacturers are equipped with robotic arms, and robots pick up parts, which greatly improves production efficiency and safety.
At present, a standard plastic pallet production line mainly includes five types of equipment: feeding equipment, mixing equipment, production equipment (injection molding machine/blow molding machine/rotomolding machine), pallet abrasive tools and robotic arms.
The site is usually equipped with turnover forklifts, cutting machines, stamping and printing machines, machine tools, spare parts and fire safety equipment.
1. Tray production feeding equipment
Before the tray is produced and processed, the raw materials need to be poured into the mixer through the feeding equipment. The feeders of different production equipment may have different models and specifications.
It should be noted that the feeding equipment should choose the appropriate size. If it is too large, it will undoubtedly increase the cost, while if it is too small, it will affect the production efficiency.
2. Pallet production mixing equipment
For mixing equipment, many people may think that it is just mixing the materials, not an important equipment.
In fact, mixing equipment is very important in plastic pallet production equipment. It needs to fully stir the materials evenly in order to produce plastic trays with bright colors and stable performance.
When producing trays, the power of the mixing equipment and the temperature during mixing must be considered.
3. Tray production injection molding equipment
For powerful manufacturers, large, medium and small injection molding machines will be equipped on the pallet production line, each of which has its own advantages.
Large injection molding machines consume a lot of energy and can produce customized large plastic trays and other plastic products. The medium and small injection molding machines are also equipped with abrasive tools of corresponding specifications and sizes, which can be flexibly processed.
Good injection molding equipment, fast and stable molding, high precision, low defective rate.
4. Tray production and processing abrasive tools
Nine-foot plastic trays, Chuanzi plastic trays, Tianzi plastic trays and double-sided trays have their own specifications and sizes, and their production abrasives are also different in structural details.
At present, the pallet abrasives of plastic pallet manufacturers have been scientifically designed and analyzed over and over again. The surface and internal structure of pallets of different sizes are slightly different, and the design of the ribs meets the load-bearing requirements of many industries for plastic pallets.
In addition, there are ingenuity of anti-slip pattern (anti-slip mat), chip card slot, heightened design, and thickened equipment, so that the tray can meet the needs of more enterprises.
5. Tray removal robot arm
In the plastic tray production equipment, the traditional injection molding machine does not have a mechanical arm, and the tray needs to be taken out manually. The efficiency is not high and the risk is strong.
At present, large injection molding equipment will be equipped with mechanical arms, robots, etc. The removal speed is faster, and the personal safety of workers is also protected.
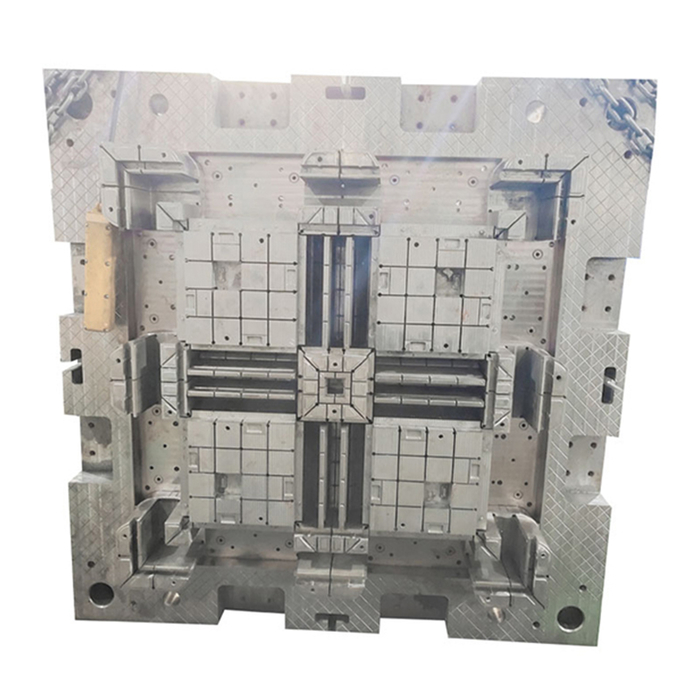
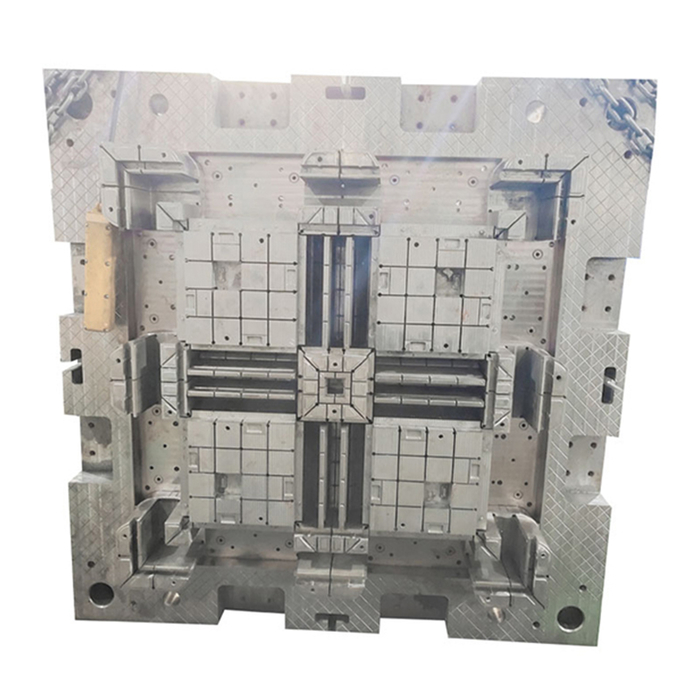
Usage:
Plastic pallets are commonly used for the commercialization of high rotation and/or bulky products. These pallets reduce the risk of damaging a product by moving it from one point to another. This is because you will only lift the platform without touching the product.
Advantage of plastic pallet:
easier to transport.safer for everyone.take up less space.more flexible and versatile.have a longer lifespan than wood pallets.